Here, we answer the question, ‘Are tents waterproof?’ Most tents these days come with claims of being waterproof – but not all ‘waterproof’ tents are made equal. Indeed, for the sake of argument, nothing with so many zips and seams and openings can be 100% waterproof. Most tents are, instead, water-resistant to differing degrees – and there is a difference. While well-made water-resistant tents do slow down the permeation of water, the fabrics can succumb to seepage of relentless, heavy rain whereas a waterproof tent would eradicate this completely.
You’ll know your tent has a good level of water-resistance if you can see liquid bead and roll off the fabric rather than be absorbed. Alternatively, if you’re soaking wet or getting dripped on in the middle of the night, you might consider that your tent isn’t particularly water-resistant, let alone waterproof.
So, are tents waterproof?
Waterproof ratings
The easiest way to check your tent’s level of water-resistance is with the waterproof rating which refers to the hydrostatic head (HH) value of the tent fabric. It measures the pressure at which water is able to press through fabric in millimeters (mmH20) and can range between 1,000mm to 10,000mm. For your reference, 1,000mmH20 is the lowest rating at which something is considered water-resistant. Beyond that, the higher the rating, the better the tent will be at reducing water permeation and protecting you from downpours.
Fabric
Tents are often made from nylon and polyester, lightweight and affordable fabrics that are not naturally waterproof or water-resistant. They are given water-resistant qualities with coatings – often referred to as Durable Water Repellent (DWR) coatings – of which there are two common types: polyurethane and silicone.
The first, polyurethane, offers water-resistance but can be damaged by UV rays and so needs regular reapplication. Furthermore, this coating will still allow water to soak through the fabric and absorb if you’re caught in a sustained downpour.
Silicone, on the other hand, is a hardy waterproof coating with a longer lifespan than polyurethane so would be the one to look out for. However, many manufacturers use a mixture of both on their tents.
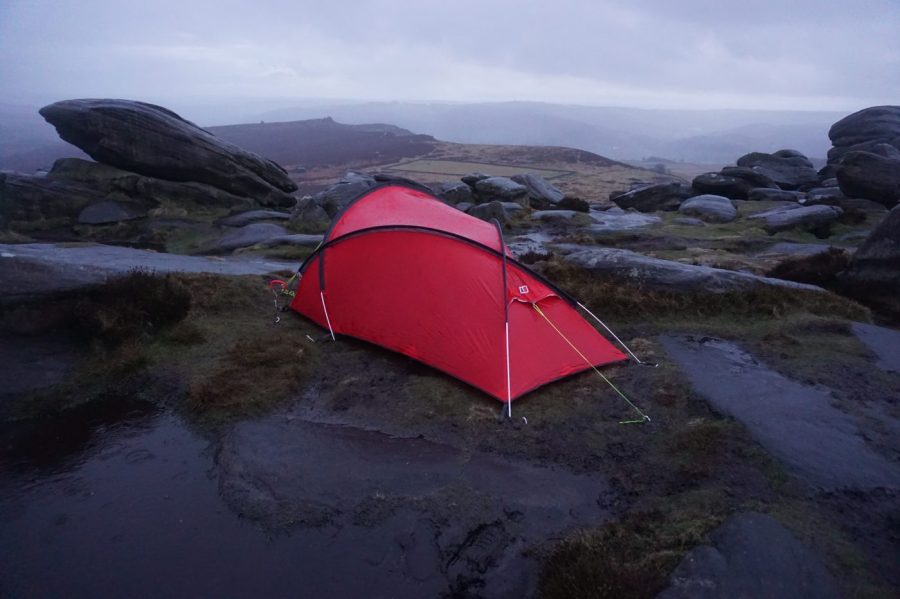
A wet night on Higger Tor. Credit: Francesca Donovan
There is a common misconception that a brand new tent is probably highly water resistant. This isn’t true and, in fact, you’d be wise to learn how to clean your tent without compromising its construction as well as investing in a good tent DWR treatment from the likes of Grangers or Nikwax to use after heavy exposure to rain or snow.
Interestingly, the traditional tent fabric of canvas does have a natural water-repellency and can be ‘seasoned’ to reinforce it by allowing it to get soaked and dry naturally, causing the weave to swell. But even canvas can also be treated with specialist waterproofing solutions inside and out to boost this natural quality and create a highly water-resistant shelter.
Sides, porches and doors aside, your groundsheet or footprint should also be tough enough to avoid rips and tears that would instantly compromise the water-resistance of your home for the night.
While the fabric’s water-resistance contributes much to the overall protection offered by a tent, it is not the only factor. Let’s take a look at seams and stitching.
Seams
Both seams and stiching are points of vulnerability in any tent, but they’re also of vital importance in holding your shelter together, especially in adverse conditions. Each stitch in your tent is effectively a tiny hole. Quality tent manufacturers will keep stitching to a minimum for this reason or use seams in conjunction with stitches to eliminate leakage.
The first, taped seams, see the tent makers heat up and melt specialist tape over the stitching – both those on the inside and out, ideally – to act like a dam and stop any water coming through stitches and getting further into the tent. Similarly, some manufacturers seal up the seams with sealant – in other words, specialist glue.
The second method joins two pieces of fabric through heat and pressure during manufacture essentially ensuring a seamless construction without any gaps or holes; these are called welded seams. Thirdly, seams can be sewn together but inverted into the tent exterior so they are less exposed to water.
It’s important to check seams – as well as any potential problem areas at ties and zips – are constructed well before taking your tent into the great outdoors and its changeable weather.